Behind the world of fluid measurement lies a seamless piece of discovery: The orifice plates. Often overlooked, this device plays a pivotal role in flow control along a wide range of applications. Let’s decode the orifice plates in detail with this blog.
What is an orifice plate?
A thin metal plate, with a small hole at the very centre, placed in an enclosed area (pipe, ducts) which acts as a hindrance or restriction to flowing fluid is an orifice plate. Paramount function of orifice plate is measurement of pressure and flow.
Why Orifice plates have a large share in flow measurement?
Reliability to its core, orifice plates are employed at places where accurate measurements are key requirements. Contributing to this, orifice plates can be applied to range of liquids and gasses. The design and installations processes for orifice plates are well documented and standardized by American National Standards Institute (ANSI) and International Organisation for Standardization (ISO). Since the number of moving parts are less, these facilitate to be a cost effective choice for integration with differential pressure transmitters. Orifice plates are compatible to variety of fluids including liquids, gasses and steam which adds up to a wide range of applications in the industry.
Science behind operation of Orifice plates:
Bernoulli’s equation is the governing principle behind the operation of Orifice plates. With increase in fluid velocity, its pressure decreases. A small hole is accurately drilled at the centre of plate which is called the orifice. Orifice plates introduce a restriction to a flow resulting in a pressure drop. Since the fluid encounters a constriction and has to pass through a small hole, its velocity rises. As stated in the Bernoulli’s equation rise in velocity results into a pressure drop facilitating measurement of differential pressure. Pressure difference between upstream side (region before constriction) and downstream side are proportional to the flow rate. Integrated with a pressure transmitter, the pressure difference is converted suitably to an electric signal which can be read from the display unit. Orifice plates act as a primary element in differential pressure transmitters. In actual practice, orifice plate is sandwiched between two flanges, around a pipe or duct as visualised from the figure.
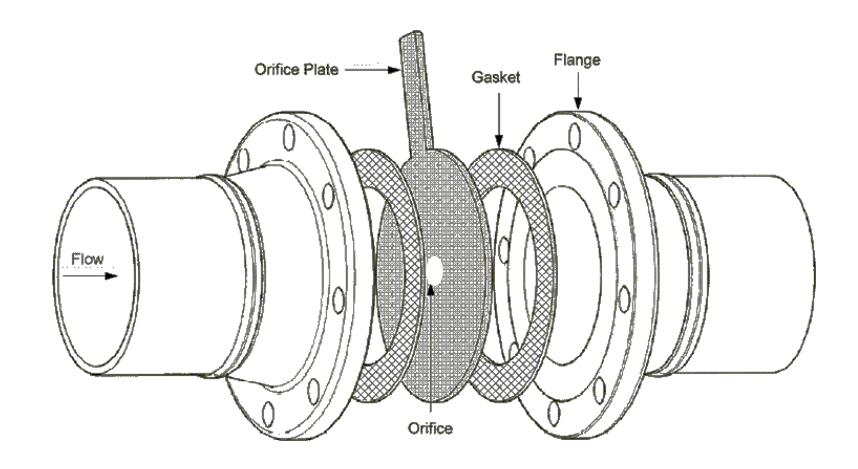
What are the different types of Orifice plates?
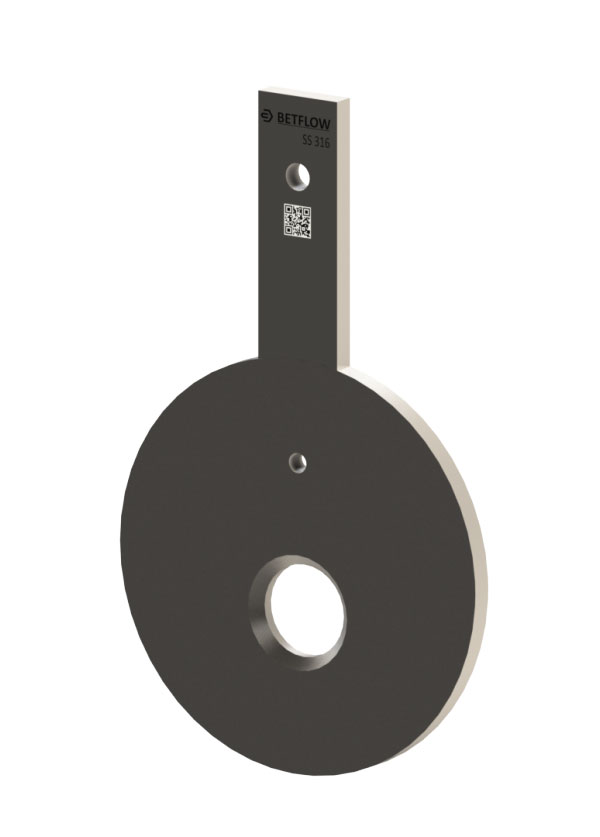
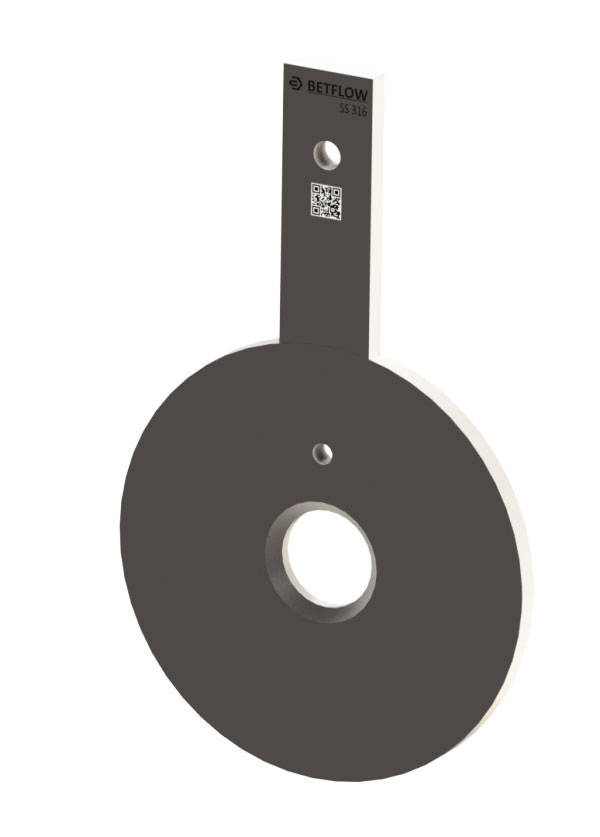
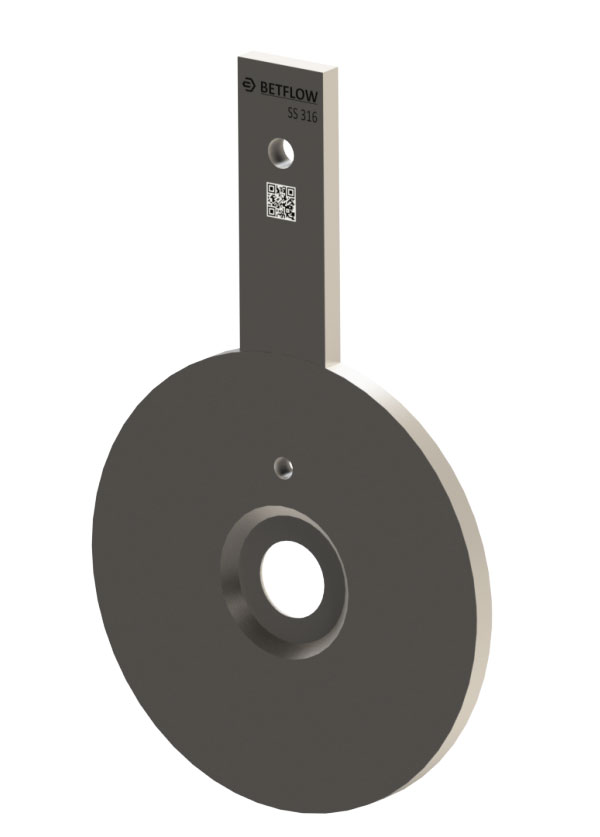
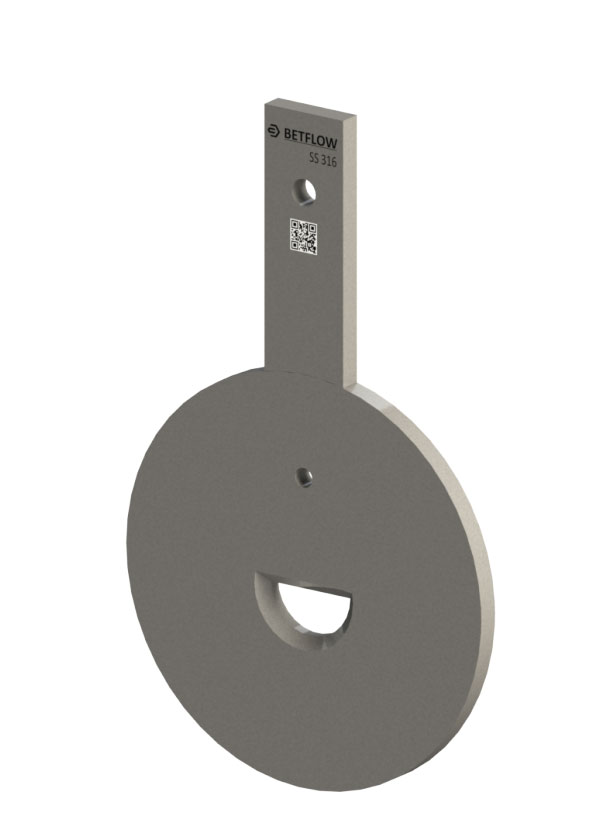
Applications of orifice plates in industry:
- Power Plants – Orifice plates are deployed in pipeline in power plant to regulate the flow to steam, gas, water to the turbines, boiler and other heat exchangers for effective performance. Since orifice plates can sustain high pressures, application in large scale, high pressure power plants is not an issue.
- HVAC systems: Orifice plates are commonly used in ducts of air conditioners in large complexes to ensure optimal efficiency of the machinery and maintain prescribed levels of human comfort in the indoor space.
- Pollution control machines: Various machines use orifice plates to monitor the gaseous pollutants by measuring the flow of gasses and the solid entrances. This helps to keep the environmental regulations under check.
- Food Industry: Consistency is the key factor in consideration for food and beverage industry. Precise determination of viscous consistency can be calculated using orifice plates.
- Water management: To maintain the levels of water quality and manage the water distribution networks, orifice plates are employed in various water treatment plants depending on the type and amount of flow.
In what scenarios segmental or quadrant orifice plates are preferred over traditional circular plate? Comment section is yours to open a discussion for the given question.